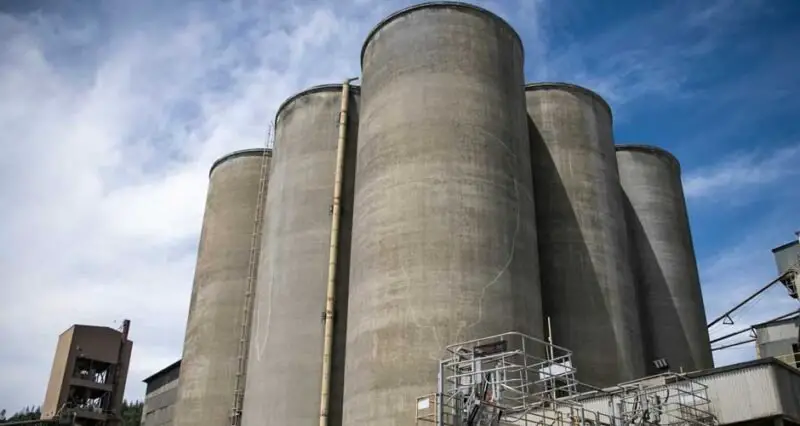
Cement, a fundamental material in construction, is responsible for about 8% of global carbon dioxide (CO2) emissions. As the world confronts the pressing and ongoing challenge of climate change, the cement industry faces increasing pressure to reduce its environmental impact.
The future of cement lies in innovative technologies and practices that are reshaping the industry, aiming to make cement production more sustainable and environmentally friendly, and with that in mind, here is an overview of how the industry is adapting to environmental challenges.
1. Alternative Raw Materials
One of the most significant ways the cement industry is adapting to environmental challenges is by exploring alternative raw materials. Traditionally, cement is produced using limestone, which is heated to high temperatures to create clinker, the primary ingredient in cement. This process releases significant amounts of CO2.
To reduce emissions, researchers and companies are experimenting with alternative raw materials that require less energy to produce clinker or that can partially replace clinker in cement. Materials like fly ash (a byproduct of coal combustion) and slag (a byproduct of steel manufacturing) are being increasingly used as supplementary cementitious materials (SCMs). These materials not only reduce the carbon footprint of cement but also improve its durability and performance.
Another promising development is the use of calcined clay as a clinker substitute. Calcined clay requires lower temperatures for processing and can reduce CO2 emissions by up to 40% compared to traditional clinker. These innovations in raw materials are crucial for reducing the environmental impact of cement production.
2. Carbon Capture, Utilization, and Storage (CCUS)
Carbon capture, utilization, and storage (CCUS) technologies are emerging as a vital tool in the cement production industry to mitigate its carbon emissions. CCUS involves capturing CO2 emissions from the cement production process and either storing it underground or repurposing it for other industrial uses.
Several pilot projects around the world are demonstrating the potential of CCUS in the cement industry. For instance, some facilities are capturing CO2 and using it to produce concrete (where the carbon is permanently trapped) effectively turning cement plants into carbon sinks. Others are exploring the use of captured CO2 to create synthetic fuels or chemicals, offering a way to both reduce emissions and create valuable byproducts.
While CCUS is still in its early stages, it holds significant promise for the cement industry, offering a pathway to substantial emission reductions.
3. Energy Efficiency and Renewable Energy
Improving energy efficiency and integrating renewable energy sources into cement production are critical strategies for reducing the industry’s carbon footprint. Cement production is energy-intensive, relying heavily on fossil fuels like coal and natural gas.
To address this, companies are investing in energy-efficient technologies, such as advanced kilns that require less energy to produce clinker. Additionally, some cement plants are transitioning to alternative fuels, such as biomass, waste-derived fuels, or even hydrogen, to power their operations. These alternative fuels can significantly reduce the CO2 emissions associated with cement production.
Moreover, integrating renewable energy sources, such as solar or wind power, into the production process can further decrease the industry’s reliance on fossil fuels. Some companies are already experimenting with hybrid energy systems that combine traditional and renewable energy sources, paving the way for a greener cement industry.
4. Innovative Cement Formulations
The development of innovative cement formulations is another area where the industry is making strides. One example is the advent of “green” cements, which are specifically designed to have a lower carbon footprint. These cements often incorporate SCMs or alternative raw materials and can be produced at lower temperatures, reducing energy consumption and CO2 emissions.
One particularly promising innovation is the development of carbon-negative cements. These cements are formulated to absorb more CO2 over their lifecycle than is emitted during their production. While still in the research and development phase, carbon-negative cements could revolutionize the industry, turning cement from a major emitter to a potential carbon sink.
5. Circular Economy and Waste Utilization
The cement industry is increasingly embracing circular economy principles, which focus on reducing waste and making the most of resources. One approach is to use industrial byproducts (such as fly ash and slag) as raw materials for cement production, reducing the need for virgin resources and minimizing waste.
Additionally, some companies are exploring the use of recycled concrete and other construction debris in cement production. This not only reduces the demand for raw materials but also diverts waste from landfills, contributing to a more sustainable construction industry.
In conclusion, the future of cement is being shaped by a range of innovative strategies aimed at reducing its environmental impact. These efforts will be crucial in meeting global climate goals and ensuring that cement remains a viable and environmentally responsible material in the years to come.