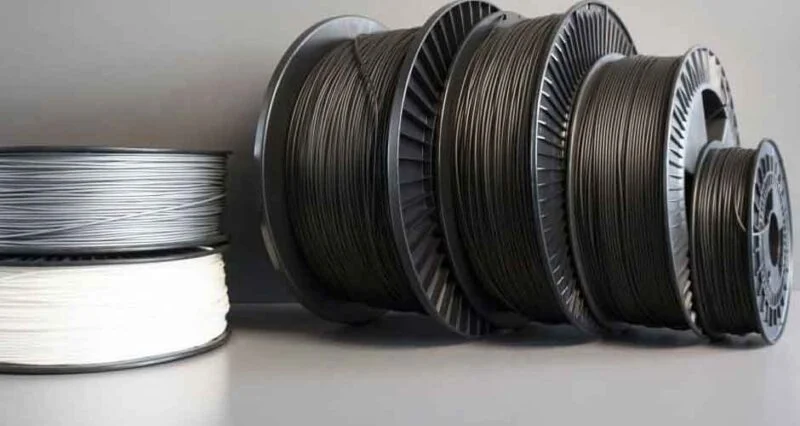
With the proliferation of 3D printing technology, PLA and ABS have emerged as two dominant materials in the field.
PLA, a biodegradable plastic derived from renewable resources, is favored for its environmental friendliness.
In contrast, ABS stands out in industrial applications due to its exceptional mechanical strength and heat resistance. Despite their widespread use in 3D printing, these materials exhibit significant differences in performance, cost, and environmental impact.
This article will provide a comprehensive analysis of the PLA vs ABS showdown, offering 3D printing users a clear guide to material selection.
Basic Description Of PLA And ABS
PLA is derived from renewable resources such as corn starch, sugarcane, or tapioca roots.
It is produced by fermenting these plant sugars to produce lactic acid, which is then polymerized into polylactic acid.
This makes PLA a biodegradable and eco-friendly material, aligning with sustainable manufacturing practices.
With a relatively low melting point of 150°C to 160°C, it’s ideal for low-heat applications but its strength and rigidity are countered by brittleness, limiting high-impact uses.
Additionally, PLA’s ability to be transparent and provide a glossy finish makes it appealing for packaging and disposable items, combining environmental benefits with functional versatility.
In contrast,ABS is a petroleum-based polymer composed of three different monomers: acrylonitrile, butadiene, and styrene.
The combination of these monomers provides ABS with its unique set of properties.
It is produced through a polymerization process that links these monomers together, creating a robust and versatile material.
ABS, with its higher melting point of 200°C to 250°C, is well-suited for high-temperature applications, showcasing notable toughness and impact resistance ideal for automotive components, consumer electronics, and toys.
Its slight flexibility allows it to bend without breaking, enhancing its manufacturing versatility.
Additionally, the ease with which it can be sanded, machined, and painted, along with the possibility of achieving smooth finishes through chemical processes, makes ABS a popular choice for creating high-quality 3D printed objects.
Characterisation Comparison Analysis
In order to better determine the suitability of these two materials for 3D printing, a complete performance comparison of PLA and ABS is essential.
Physical and Mechanical Properties
- Strength and durability
ABS outperforms PLA in terms of strength and durability, which makes it more suitable for applications that need to withstand higher levels of stress and impact, such as automotive parts and consumer electronics.
PLA, while also offering good rigidity, is more fragile and therefore may not be the best choice for applications requiring high impact strength.
- Flexibility
ABS shows better flexibility and can withstand some degree of bending without breaking. PLA, on the other hand, is harder and more brittle and tends to break when subjected to strong forces.
- Thermal stability
ABS is more thermally stable than PLA, with a higher melting point (200°C to 250°C) and deflection temperature.
This makes ABS more suitable for applications that may be exposed to higher temperatures.
In contrast, PLA’s lower melting point (150°C to 160°C) limits its use in high-temperature applications.
Processability
- 3D Printing Suitability
Both PLA and ABS are widely used for 3D printing, but PLA’s low melting point and lack of need for a heated bed make it easier to print for beginners and home users.
ABS, while offering higher strength and temperature resistance, requires a heated bed and good ventilation when printing to avoid warping and the release of harmful gases during the printing process.
- Processing parameters
PLA typically prints at temperatures between 180°C and 220°C, while ABS prints at temperatures between 210°C and 250°C.
ABS may need to be printed at relatively slow speeds to prevent warpage and ensure good bonding between layers.
- Post-treatment needs and methods
PLA prints can be post-treated by a variety of methods, such as sanding and painting, to improve appearance.
ABS prints, in addition to these treatments, can be vapour smoothed with solvents (e.g. acetone) to achieve a smoother surface.
This is particularly suitable for applications requiring high surface quality.
Environmental And Health Impacts
As a bioplastic derived from renewable resources, PLA has relatively lower carbon emissions during its production process.
More importantly, it is biodegradable under industrial composting conditions, reducing long-term environmental impacts. Thus, from an eco-friendliness perspective, PLA is often considered a more preferred material.
Moreover, PLA is deemed safe under normal usage conditions. Due to its biodegradability, PLA does not accumulate in the environment over time, minimizing potential threats to ecosystems and human health.
In contrast, the production of ABS relies on petroleum, implying a potentially higher carbon footprint throughout its life cycle.
Although ABS exhibits excellent performance during its usage life, it is not biodegradable, necessitating recycling or other management methods post-use to mitigate environmental impacts.
Notably, ABS may release harmful gases, such as styrene, especially during 3D printing, requiring well-ventilated conditions to minimize risks.
This comparison underscores the environmental contrasts between PLA and ABS, further highlighted in the ABS vs PVC debate, where both are petroleum-based but ABS is generally seen as having a less detrimental environmental and health impact compared to PVC.
Other Application Cases
Having learned about the various properties of PLA and ABS, you might be wondering in which fields these materials can be applied. Let’s explore this together.
PLA, with its non-toxic and biodegradable characteristics, is used to manufacture a variety of consumer goods, including toys, office supplies, and garment fibers.
For brands pursuing sustainability, PLA also serves as an ideal choice for food packaging and disposable cutlery. Additionally, due to its excellent biocompatibility, PLA is utilized in creating absorbable sutures, drug delivery systems, and biomedical implants.
Thanks to the durability and safety of ABS, it becomes the perfect material for manufacturing toys, with LEGO bricks being the most iconic application.
In the automotive industry, ABS is extensively used for interior and exterior vehicle components, including dashboards, door handles, and bumpers, due to its high strength and heat resistance.
Many consumer electronics casings, such as those for mobile phones, TV remote controls, and computer accessories, are made from ABS.
Conclusion
Overall, PLA and ABS each have their strengths, allowing them to excel in different application areas.
For beginners, PLA material is easier to print with and has less stringent requirements for the printer compared to ABS.
However, for 3D printing projects that require high strength, durability, or specific mechanical properties, ABS is a good choice.