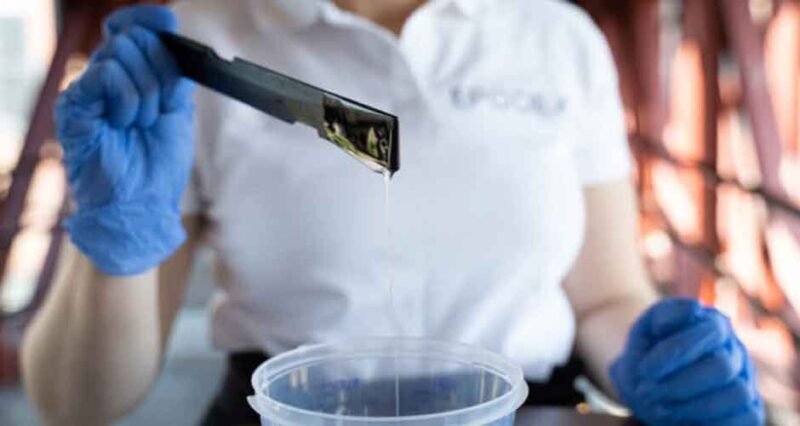
When it comes to creating strong bonds in the manufacturing, construction and woodworking industries, or even DIY projects, repair works and restorations, few adhesives can match the outstanding properties of epoxy which is known for its extraordinary reliability under pressure. This would explain why, in addition to being among the primary choices of adhesives for both commercial and residential purposes, Five Star Management professionals say this material is also often the perfect candidate for protective coatings and fillings in a range of products.
What Are Important Facts About Epoxy Resins?
Well, first and foremost, the aspect of them being structural adhesives, given that they become part of the very thing they bond to. The glue is a creation of the process of blending the epoxy resin as a synthetic polymer with chosen additives and hardeners (e.g. amines) which, depending on the application, can affect the pot life and curing times accordingly. The result of the blend can either be one-part or two-part epoxies depending on when they’re blended, with a resin-to-hardener ratio of 1:1, 2:1 or 4:1.
When the blend happens separately, without the need to cure them at elevated temperatures, what you have is the two-part adhesive which offers more flexibility for a DIYer. As for the one-part epoxy alternative, the resin and the hardener already come blended so you don’t have to take care of any dosing, mixing, or air-bubble removing, but to be able to cure them you require an elevated temperature. The difference is also in the time it takes to cure, with the two-part taking much faster.
The chemical reaction of mixing these two components offers an epoxy resin glue product that’s famous for its remarkable durability, strength, and adhesive substance. The minute you find yourself working on a project that involves the use of this type of adhesive, you come to realise there’s more than one type to choose from, and it all comes down to what it is you require. Basically, the choice falls between glycidyl and non-glycidyl categories.
Out of these, the glycidyl care glycidyl-ether, glycidyl-ester, and glycidyl-amine varieties, whereas the non-glycidyl are aliphatic and cyclo-aliphatic. With differing properties, like viscosity and colour, it’s understandable each comes with its own advantages for specific uses and industries. Categorised by the chemical chain the epoxy is bonded to, you can commonly find them as:
Bisphenol Epoxy Resins
Formed by a reaction between bisphenol-A and epichlorohydrin, this and glycidyl-ether bisphenol-A (DGEBA) epoxy resin glue is an adhesive product common with the lowest molecular weight perfect for various commercial applications as well as residential-like structural bonding of concrete.
Glycidyl-amine Epoxy Resins
The product, created with the reaction between epichlorohydrin and aromatic amines, has got signature low to medium viscosity at room temperature, and as such is fit for easy processing.
Novolac Epoxy Resins
Created by the reaction between phenol and methanol, the result is a glycidyl residue such as epoxy cresol novolac (ECN) and epoxy phenol novolac (EPN) with are free of volatile organic compounds. Thanks to the improved strength of the cured system and the incredible chemical resistance, this specific epoxy resin glue type is perfect for high-temperature applications.
Halogenated Epoxy Resins
Created with a mixture of brominated and fluorinated varieties, you get a resin product that’s great for application in electrical projects, like those where you require flame resistance.
Epoxy Resin Diluents
Created with the glycidylation of polyols or aliphatic alcohols, the diluents can be monofunctional, difunctional, and of greater functionality.
Aliphatic Epoxy Resins
These are created by either double-bond epoxidation (e.g. through vegetable oils and cycloaliphatic epoxides), or a reaction with epichlorohydrin (e.g. glycidyl esters and ethers). Out of the two options, it’s the cycloaliphatic epoxy adhesive resins that are desired for the distinct structure that is high in oxirane and low in chlorine. As such, these are ideal for their low viscosity, low dielectric constants, weather resistance, and high glass transition temperature (Tg).
Another distinction they fall into is two categories: coatings, and casting. The coating resin type takes less time to cure. As such, the coating varieties are tougher, harder, rigid and thick even in thinner layers, as opposed to the casting which happens to be more flexible. Be sure to read the descriptions of products online, or the labels on them in case you’re buying in-store so you get what you need for your project if you choose to use one of these incredible resins for your DIYing.
Is Epoxy Resin a Good Glue?
Considering its viscous nature, quick curing, and the fact it adheres to a range of surfaces, whether they’re of metal, some types of plastic, wood, glass, stone, or even concrete form, it’s safe to say epoxy makes for a great adhesive. Once you’ve done the mixing right (if it’s the two-part type), and have waited out the suggested curing time, you can count on incredible strength, minimal to no shrinkage, solvent and chemical resistance, as well as low toxicity as I mentioned some options don’t have VOCs.
Due to its chemical varieties, among which even cyanoacrylate, polyurethane, and acrylic, it’s an adhesive that’s the best of the best in industries of all kinds, including aircraft, automotive, sports (e.g. gluing parts of sporting goods like bikes, skis and snowboards), carpentry, woodwork, electric and jewellery making alike. All this besides being an exceptional choice for home projects.
In short, anywhere where it’s necessary to get bonding that’s tough and can withstand some wear and tear from moisture and weather. The epoxy glue is equally great for use with dissimilar objects, i.e. those that differ in the material, so you can just as easily bond metals with certain plastics, for example, and count on a strong grip.
Mind you, I said certain, because plastics you shouldn’t use this type of adhesive with are LSE (low surface energy). Despite its relatively fast curing time, it’s advisable to do some slow curing of the resin in warmer conditions if this project is of high importance as this would create even stronger bonding.
Other Uses of Epoxy Resin
The adhesive application isn’t the only area where epoxy gives out a stellar performance – there’s its use in industrial tools, specifically the creation of casting and injection moulds, insulators, generators, and even motors, component fixtures and prototype models. There’s also its use in construction for filling in cracks and restoring structural integrity.
As such, it’s highly beneficial for paints, sealants, and coatings thanks to its highly protective and insulating properties which make it great for the reduction of damage from impact. Furthermore, it’s the perfect solution for repair and maintenance work, like fixing concrete driveway cracks, due to its many beneficial properties mentioned previously.
And, don’t worry if you have some left over after the repairs and maintenance – you can always think of creative ways to use it up to create unique artwork and jewellery! Just remember to follow the instructions on how to properly use this type of product to ensure you get the desired results. Also, maintain your safety at an all-time high with the appropriate PPE like nitrile gloves, a mask (if not working with no VOC resin), safety goggles, and some wipes at hand to effectively clean up spills.