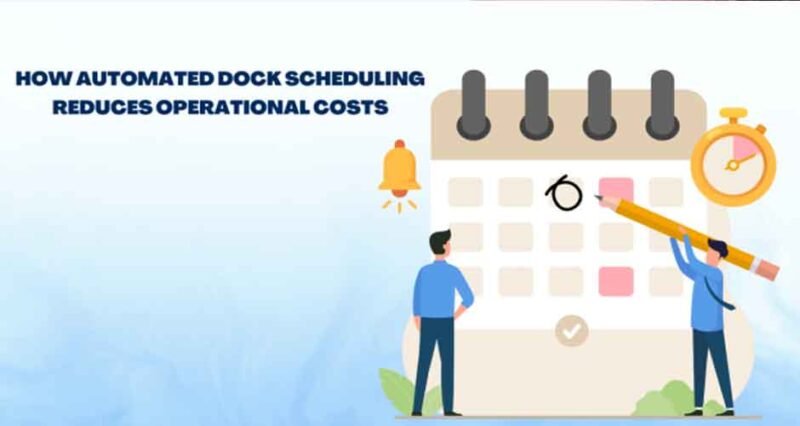
Efficient operations are the foundation for successful supply chain management. With tight margins and fierce competition nowadays, Companies must optimize every process to reduce costs. One prime target for automation is dock scheduling – a huge impact on the bottom line. Let’s examine how automated dock scheduling saves money by significantly improving operational efficiency..
The Role of Automated Dock Scheduling
Loading docks are a crucial bottleneck and cost-center in warehouse operations. Efficient dock scheduling is crucial for optimizing asset utilization and preventing congestion, long wait times, and logjams. But old methods like whiteboards, spreadsheets, and tribal knowledge are inefficient.
Scheduling managers spend hours upon hours coordinating and sequencing shipments based on factors like destination, priority, open docks, and more. It involves constantly adjusting plans to manage delays, traffic congestion, and unexpected issues. Attempting to manually optimize dock usage makes it challenging to fully utilize assets and maintain a high-speed operation The costs of manual inefficiency only go up from here.
Automated dock scheduling is a game changer with real-time visibility into open dock doors and advanced algorithms to optimize usage and sequencing. By reducing manual mistakes and conflicts while adapting to constraints, automation pumps up operations. Automated systems sync up with warehouse management, transportation management, yard management programs, and more to align planning enterprise-wide.
According to Gartner, automation can save scheduling time by up to 90% compared to manual methods. This proves that automation produces tremendous productivity gains. With real-time updates on dock availability, truck wait times can be reduced by 50% or more through optimized usage.
One significant advantage of automated scheduling is the reduced need for constant human oversight and manual adjustments. This frees up staff to focus on more important stuff than schedule juggling.
The future of high-speed docks is tapping optimization algorithms and automation to do the heavy lifting. This leaves people to handle tasks that algorithms can’t like relationship management, exception handling, and continuous improvement.
Benefits of Automated Dock Scheduling
By leveraging advanced loading dock management software, this automated approach streamlines and optimizes the scheduling of shipments, arrivals, and departures. Automated dock scheduling delivers quantifiable benefits that reduce costs and boost productivity:
Cost Reduction
By minimizing manual scheduling labor and coordination, automated scheduling can decrease labor costs by 15%. Optimization reduces truck wait times, resulting in 20% lower overtime expenses from fewer delays. Intelligent scheduling maximizes asset utilization, leading to savings.
Improved Efficiency
Automation enhances warehouse efficiency. Truck waiting times are reduced by an average of 45 minutes per load, enabling faster turnarounds. Overall operational efficiency climbs by 30% as dock congestion is minimized through optimization algorithms.
Enhanced Customer Satisfaction
Customers value fast and reliable deliveries. Ninety-five percent of customers consider on-time deliveries critical for satisfaction. Automated scheduling delivers, reducing delays. The result is greater customer retention and loyalty. Delivery delays can lead to 25% higher customer attrition rates.
Integration with Other Systems
To maximize the benefits of automated dock scheduling, integration with related supply chain systems is critical. This integration provides holistic visibility across the logistics ecosystem and allows various systems to share real-time data to improve scheduling agility, accuracy, and efficiency.
Tight integration between the automated dock scheduling system and warehouse management system (WMS) enables seamless execution of scheduling decisions on the floor. As items are picked and staged for loading, the WMS can share real-time updates that allow the scheduling system to adjust dock assignments.
Integration with Transportation Management Systems (TMS) and yard management software provides end-to-end visibility from yards to docks. Real-time tracking of incoming trucks and trailers from the yard enables precise dock assignments. Traffic and congestion data improves ETAs and scheduling agility.
Insights from inventory management tools allow scheduling around item availability and priority. Slow-moving items may be scheduled for end-of-day dock assignments, while high-priority SKUs can be fast-tracked.
According to Accenture, 84% of companies report improved supply chain visibility and control through system integration. With modern API-driven integration between dock scheduling and related systems like WMS, TMS, ERP, and inventory management, businesses gain improved logistics visibility and efficiency.
Overcoming Implementation Challenges
Transitioning from entrenched manual processes to automated dock scheduling requires addressing common challenges:
Resistance to Change: Employees accustomed to legacy whiteboard/spreadsheet scheduling may initially resist the switch to automation due to fear of the unknown. Clear communication of the benefits, ample training on the new system, and proactive change management will help ease the transition. Phased implementation and support during the transition are key.
Technical and Integration Hurdles: Legacy IT systems and outdated infrastructure can pose technical obstacles to seamless integration. Prioritization of new capable software, APIs, and hardware upgrades is crucial. Bringing in the right technology partners ensures smooth and rapid integration.
Data Accessibility Issues: Automated scheduling relies on real-time data from sensors and systems. Network connectivity blackspots, incomplete data, and accessibility issues will need remediation.
Unoptimized Business Processes: To reap the full benefits, associated business processes may need redesigning. Current processes developed around manual scheduling may be suboptimal for automation. Streamlining processes boosts ROI.
Insufficient Buy-In: To achieve company-wide adoption, it’s essential to gain buy-in at all levels. Building credibility involves demonstrating success through pilot programs. Executive mandate and encouragement ease adoption.
With upfront planning, investment, and mitigation of these challenges, the transition to automated scheduling can be smooth. The long-term efficiency gains justify the effort of overcoming initial challenges for forward-thinking businesses.
Conclusion
Automated dock scheduling delivers game-changing operational efficiency and cost savings through optimization algorithms and system integration. Transition hurdles can be systematically addressed. Considering the quantifiable benefits, ranging from reduced labor costs to improved customer satisfaction, businesses should seriously consider implementing automated dock scheduling to enhance their competitiveness. The future of supply chain success entails harnessing cutting-edge technologies such as automated dock scheduling.
FAQs
How quickly can I expect a return on investment in automated scheduling?
Most businesses experience significant reductions in labor costs within six months and can recover software and implementation expenses in less than two years.
What types of businesses benefit most?
Distribution centers, 3PL warehouses, and manufacturing facilities with time-sensitive operations see the greatest impact. But most multi-dock operations can benefit.
Is transitioning complex in automated scheduling?
With careful planning and phased implementation, the transition can be relatively smooth. Training and testing minimize disruptions. Transition support from vendors also helps.