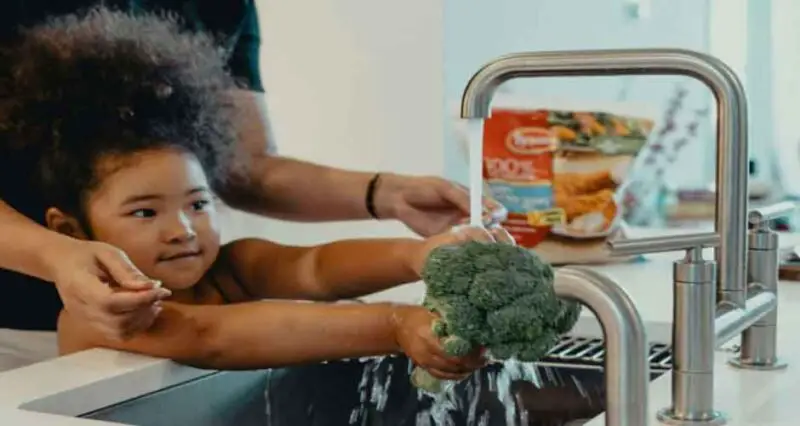
The water purifier filter market is projected to surge to USD 54.48 billion by 2030, propelled by commercial and industrial demand. Among the factors driving this growth is the increasing popularity of filter types like pleated filter cartridges. These filters are favored for their precision filtration, particularly in industries such as pharmaceuticals, food and beverage, and water treatment. They ensure high product quality by effectively removing fine particles.
The cartridges utilize a pleated structure to prevent sediments, allowing them to hold a substantial amount. They come in various materials, including PP, Glass Fiber, Nylon, PES, PTFE, and PVDF, and can be hydrophilic or hydrophobic.
To learn more, continue reading. In this blog post, we’ll delve deeper into their construction, benefits, replacements, and maintenance. Let’s get right into it!
Production Process
Pleated filter cartridges comprise various components, including filter membranes, non-woven fabrics, long fibers, support nets, inner cores, outer cages, end caps, and sealing rings. The manufacturing process follows the following sequential steps below:
1. Membrane Pleating
The membrane pleating process starts with the stacking or piling of filter media, including membranes, non-woven fabrics, and long fibers. Next, a specialized machine is used to pleat these layers. Following that process, the media is precisely cut to meet the required membrane area specifications for the cartridges.
2. Ultrasonic Edge Seam Welding
In ultrasonic edge seam welding, the cut material gets welded along its edges using a special machine. This welding seals the edges, making a strong ring shape. This keeps the material whole and stops leaks when filtering.
3. Ultrasonic Hot Melt Welding
In this phase, a machine joins filter cartridges or connects the filter element to the end cap. This creates a strong connection, improving filtration and stopping leaks.
The rigorous manufacturing processes employed in the production of pleated filter cartridges ensure their compliance with stringent quality standards. This makes them dependable solutions for diverse industrial filtration applications.
Why Use Pleated Cartridge Filters?
Pleated membrane purifiers effectively intercept pollutants on a single plane using the membrane, therefore offering better efficiency than melt-blown and string-wound purifiers that capture impurities through their internal structure. Below are some specific advantages
Superior Filtration Capacity
These filtration devices employ a surface filtration method, where pollutants are directly intercepted on the membrane’s surface. The evenly distributed membrane pores ensure consistent filtration, preventing particle leakage even during pressure fluctuations. This is a key feature when comparing pleated vs non pleated deep filtration methods. For example, devices like melt-blown and string wound cartridges, in contrast, may allow particles to bypass the filter medium, compromising efficiency.
Improved Filtering Effects
The water purifiers are capable of achieving a more precise filtering effect compared to other types of purifiers. The membranes are crafted from polymer chemical materials through advanced technology. This allows for the creation of smaller pore sizes, ensuring the removal of even finer particles from the fluid stream. In contrast, deep filtration elements rely on larger sieve holes throughout the medium, which may not capture particles as effectively.
A Greater Degree Of Flexibility
The design of the device offers greater flexibility in filtration applications. They can be composed of one or more layers of membranes, long fibers, and non-woven fabrics with varying filtration precision. This versatility enables their use across a wide range of industries and applications, providing tailored solutions to specific filtration needs. In contrast, the limited variability of deep filter elements may restrict their suitability for diverse filtration tasks.
Replacement Process
Change the filter housing when the pressure gauge reaches the recommended pressure to avoid damage to the device. Here are the steps to follow:
- Ensure you have a brand-new cartridge with the correct specifications.
- Close water inlet and outlet valves to stop the system. Slowly open the exhaust valve to relieve pressure.
- Open the drain valve slowly to let the liquid drain out of the filter housing.
- Open the cover, remove the old device, and clean the housing.
- Moisten the O-ring with lubricant and insert the new filter vertically into the socket. Ensure the O-ring and socket are in complete contact.
- Install and secure the filter platen, close the top cover, and tighten the bolts.
- Close the drain valve, open the water inlet valve, and let liquid enter the housing. Close the exhaust valve once the liquid overflows. Slowly open the outlet valve fully, then adjust the inlet valve to reach the initial pressure difference.
Maintenance Procedure
- Check the device for damage, wear, or clogging, and replace cartridges as needed.
- Clean clogged devices to restore their effectiveness. Follow manufacturer guidelines for proper cleaning methods.
- Store in a clean, dry, and sterile environment when not in use.
- For sterile environments, use clean, dry saturated steam to sterilize the filter before use.
- Always follow the manufacturer’s recommendations for maintenance procedures.
Conclusion
Pleated filter cartridges stand out as dependable solutions for diverse industrial filtration needs. With their rigorous manufacturing processes and advanced technology, these cartridges offer higher efficiency, precise filtering, and flexibility. Trustworthy brands like Filterway ensure quality and reliability, making them the preferred choice for maintaining optimal performance in purifier systems.